Monogram Food Solutions LLC, headquartered in Memphis, Tennessee, USA, is a producer and distributor of packaged meat products, snacks, and appetizers. The rapidly-growing company’s products include beef jerky, sausage, hot dogs, pre-cooked bacon, and pet treats, among other processed food items.
Challenge
Monogram’s FDA-approved pet food manufacturing plant in Schulenburg, Texas, USA, makes meat-based pet treats that contain no artificial ingredients or filler. The pet treats are such high-quality that they are fit for human consumption. Monogram wanted a wastewater treatment system of the same superior caliber.
At the time, the plant was skimming oil before discharging its wastewater to a municipal treatment system—but that came at a price. Moreover, new production lines at the plant resulted in a significant increase in wastewater flow and load, which would exceed treatment capacity at the municipal plant.
Solution
ADI Systems was selected to design, construct, and commission an on-site wastewater treatment solution for Monogram’s pet treat plant. The technology of choice was a ADI® membrane bioreactor (MBR), an innovative aerobic technology that uses a submerged physical membrane barrier to provide the liquid/biosolids separation.
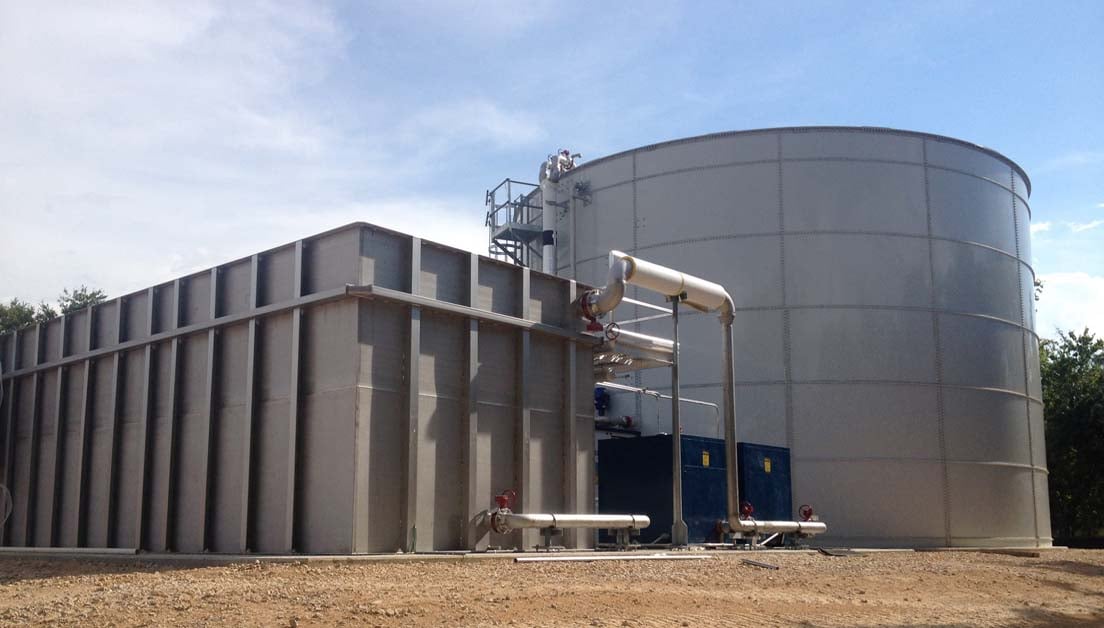
Monogram’s wastewater contains high concentrations of fat, oil, and grease (FOG) resulting from animal fat and cooking oils. Because of this, care had to be taken in the design of the membrane-based biological wastewater treatment system to ensure there would be no long-term issues with foaming, biological performance, or membrane fouling.
The contract completion date was scheduled for October, but ADI Systems’ ambitious project management team projected a late-July start-up date. The team is proud to have successfully met this goal, designing and constructing the treatment plant in less than four months.
Results
The system treats all Monogram wastewater and generates a pristine effluent typical of ADI® Systems’ MBR technology. Engineered to be the simplest, most reliable MBR technology available on the market, the system is designed to remove over 99% of Monogram’s influent biochemical oxygen demand (BOD). An up-front grease trap is used to collect and remove a portion of the FOG in the wastewater; however, the majority of the FOG (design concentration of 260 mg/l) is digested in the MBR system.
The long solids retention time and near-perfect solids capture results in enhanced process stability and complete nitrification. The submerged membranes generate a solids-free effluent with very high membrane uptime and minimal maintenance. Even when treating high-strength wastewater, the MBR system maintains a low membrane fouling rate with infrequent membrane cleanings, simplifying the overall treatment system operation.
The MBR system supplied by ADI Systems for Monogram has met the objectives in terms of construction and installation timeline, simplicity of operation, and effluent quality.