Mobile Deionization and Service Deionization
See All Ion Exchange ServicesDeionized water is essential for applications throughout different industries, from power and refining to chemical manufacturing and food and beverage. Mobile deionization ensures rapid response when you have system changes or expansions but don't need permanent installations, and service deionization ensures consistent uptime through scheduled service. For a detailed data sheet, click here.
- is the minimum order quantity for this product. Please check quantity and add to cart again.
or reach out for more information about our mobile solutions .
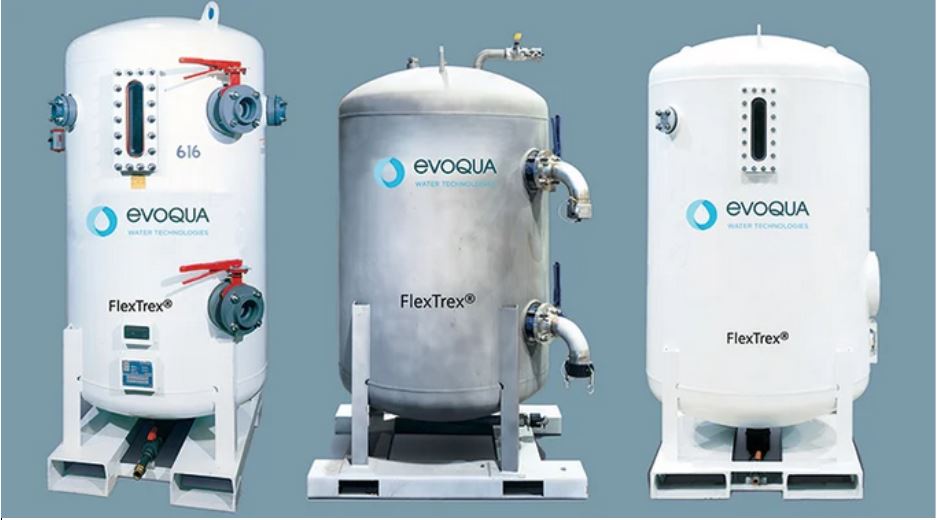
Deionized water is essential for applications throughout different industries, from power and refining to chemical manufacturing and food and beverage. Mobile deionization ensures rapid response when you have system changes or expansions but don't need permanent installations, and service deionization ensures consistent uptime through scheduled service. For a detailed data sheet, click here.
or reach out for more information about our mobile solutions .
Discontinued productDescription
Deionized water is essential for applications throughout different industries, from power and refining to chemical manufacturing and food and beverage.
Whether the deionized water you’re using is generating steam or cleaning your PVC panels it serves a vital role to your process and it’s important that your equipment can operate efficiently and effectively for long periods of time while also meeting your effluent requirements.
Deionization ensures the reduction of multiple contaminants like TDS, Silica, chlorine, hardness, and many others. This method is designed for applications such as water softening, boiler feedwater, condensate polishing, zero liquid discharge (ZLD), and many more. Our Mobile solutions ensure uptime and meet your product water specifications. Our services can range from tackling immediate needs and emergencies through our 24/7 Mobile dispatch to providing a scheduled service each month.
Do you have a scheduled shutdown?
With our mobile service, we can ensure a consistent supply of deionized water. Evoqua provides this mobile service by providing and exchanging vessels in a range of sizes depending on application and flow rate. We also provide trailer-sized units which can be installed on site for a pre-determined time. Our resin is regenerated off site at our regeneration facility where we have available assets ready to be exchanged.
Learn about our other temporary capabilities for shutdowns, and planned maintenance events (Shutdowns & Turnarounds).
Already have a permanent system?
In addition to our mobile service, we also provide resin regeneration as a service. That means we can take spent resin and regenerate it off-site and deliver fresh resin.
Having an emergency that requires Deionized water quickly?
Evoqua provides a 24/7 mobile dispatch team dedicated to taking care of our customers at a moment’s notice. We understand your urgency and with our readily available assets, we can provide a rapid response.
Are you discussing capacity or plant expansion plans?
Based on your incoming feed water we can design a unique and effective solution to fit your current system’s flow rate and treatment goals.
What are your effluent requirements?
Whether you are looking to reduce total hardness, conductivity, or silica, Evoqua offers a variety of effective media and resins to help reach your product water specifications. Proper regeneration is critical for optimum performance, exchange capacity, total volume output, and low operating cost. Our quality control specialists carefully pretest, then select only resin lots that meet our stringent requirements, assuring you maximum performance with every exchange.
Quality
There are no shortcuts to quality
- Incoming quality control: Raw materials must meet quality specifications
- In-Process quality control: Each component has its own operating criteria, and the entire process is monitored.
- Final Product quality control: Materials are double-checked for quality with results recorded in the batch record
- Each service unit is chemically sanitized before refilling
Ask about some of our other service capabilities
- Interim use until a permanent system is installed
- RO Polishing
- Process water quality changes
- Seasonal water needs
- Membrane services
- Sanitation services
- Carbon services
- Service deionization
Our schedule fills quickly so give us a call or request a proposal today!
24/7 mobile dispatch: (800) 435-3223
Documentation
- MOSS-MODI-DS-0724.pdf1.1 MB
- WWIX Media Product Guide337.7 KB
- Wastewater Ion Exchange Services Brochure844.2 KB